The adhesives and sealants industry is helping to power the transition towards a greener future, one where renewable energy dominates. At Permabond, we’re proud to be a part of this transition. Whether it’s adhesives for bonding hydrogen EV fuel cells, electric motor magnet bonding for EVs, or even products for wind turbine repairs, our broad product palette can help green-minded designers and engineers bring the future into the present.
Hydrogen Bonding – A Challenge No Longer
Hydrogen-powered vehicles, otherwise known as hydrogen fuel cell vehicles (HFCVs), are becoming increasingly popular. These vehicles offer all the benefits of an EV, such as greatly reduced carbon emissions as well as lower costs associated with owning a vehicle, such as road tax, congestion and parking charges. However, unlike traditional EVs, refilling a hydrogen fuel cell takes only a matter of minutes, making them much more convenient to use, and they tend to have a longer operating range, thus reducing ‘range anxiety’ associated with EVs. The other major benefit is that hydrogen fuel cells are recyclable, further reducing their climate impact. The global market value for HFCVs is estimated to reach $42 billion by 2026.
There are multiple applications for adhesive within HFCVs. These range from bonding the fuel stacks together, to the fuel cell casing and the connectors linking the cell to the rest of the vehicle. However, there are inherent challenges when bonding around hydrogen. Hydrogen has the smallest molecules of any element in existence. These molecules are also very ‘seeking’ and highly explosive. Due to their miniscule size, hydrogen atoms can easily seep into metals, making these more brittle and eventually leading to stress cracking or fractures. It is therefore of paramount importance that any adhesive used in an application coming into contact with hydrogen is able to offer a completely tight seal to both prevent this embrittlement, and also reduce the risk of explosion.
[
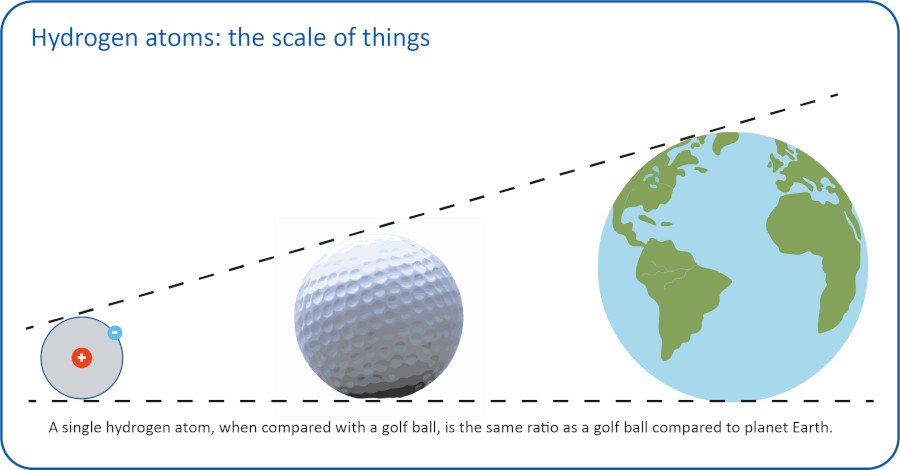
In 2022 Permabond launched F201HV, a toughened anaerobic adhesive designed with hydrogen sealing front of mind. Approved for use by gas testing organisation Kiwa, this product meets the requirements of Inorm KE214 for hydrogen gas safety, forming an incredibly tight seal on metal bonded parts. Due to its core-shell toughening, it isn’t brittle like conventional anaerobic adhesives. Instead, it offers a high degree of flexibility which makes it ideally suited to bonding dissimilar materials, as it can comfortably handle differential thermal expansion and contraction. F201HV is therefore highly suited to bonding HFCV fuel cell fittings, as these need to have an impenetrable seal to prevent any leakage of hydrogen, as well as being able to withstand frequent changes in temperature.
Adhesives – the way forward for EV Motor Magnet Installation
Electric motors are a key component in EVs, helping to drive the car by using power generated by the battery to turn the wheels. Most magnets used in EV electric motors are permanent due to their constant magnetism, capacity for increased vehicle range and lightweighting capabilities. Of all materials used for these magnets, neodymium is the material of choice for most EV manufacturers due to its magnetism being the most powerful available commercially as well as its high energy density, which allows for smaller motors.
There is a wide range of options that manufacturers may consider for installing their magnets into the electric motor housing. Some popular methods include press fitting, where the magnets are pressed into machined slots in the rotor or stator, as well as welding and injection moulding, whereby the magnet housing is effectively shaped around the magnet mould using molten material. Then of course, there is the option to use adhesives to bond the magnets in place.
Since neodymium is the magnet material of choice in EVs, great care needs to be taken when choosing the best installation method. Neodymium is brittle by nature and can easily crack or break under stress. These magnets also have poor heat resistance, with subjection to too much heat potentially leading to a change in magnetic properties, or even complete demagnetisation of the magnet. Such an event would render the costly magnet effectively useless. With this in mind, all three of the above-mentioned installation methods come with risks – press fitting exerts a lot of stress onto the magnets and welding creates a lot of heat, as does injection moulding. Adhesives present a safer, more gentle option that does the job required just as well, with none of the risk involved.
Permabond offers a range of adhesives suitable for bonding neodymium in EV motor magnets to the rotor or stator core. These products provide a strong, resilient and lasting bond on both neodymium as well as other magnetic materials. They also offer great temperature resistance and a quick cure, making them great for high-speed production lines.
Prolonging Wind Turbine Life
With the world in the grip of a climate crisis, it’s never been more important to focus on green energy solutions than it is now. One such solution is wind-generated power, which has become vastly more popular over the past few decades. Indeed, wind power is now one of the fastest-growing renewable energy technologies worldwide. 26.8% of the UK’s electricity generated in 2022 came from wind power alone – a significant achievement.
With this growth in the use of wind energy comes an increase in demand for wind energy adhesive technologies. Adhesives can increase production speeds and reduce material weight, which, for example, can help extend turbine blade design options. In addition to this, using the right adhesive can improve the quality and lifespan of these blades, including facilitating repair work. This has a direct environmental impact, as blades are often not recyclable.
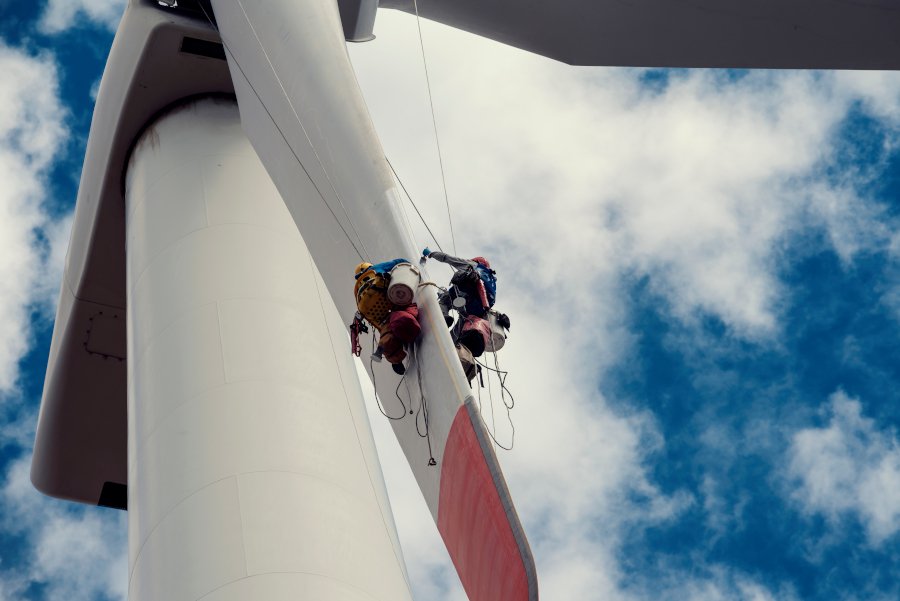
Generally speaking, the use of thixotropic adhesives, particularly 2-part epoxies, is standard in turbine blade bonding. This is because the two components of these adhesives – the resin and hardener – develop ‘non-slumping’ properties quickly after mixing. A slow-curing, fast-exotherm adhesive tends to be best, as these allow maximal working time, yet a fast cure once set in place. These adhesives also provide very high levels of impact, temperature and weather resistance, all essential qualities for wind turbines, which must be able to withstand harsh conditions throughout their lives.
Permabond has experience in wind turbine repairs and has recently launched a new ultra fast-curing, two-part epoxy adhesive which is ideally suited to repair work. Offering outstanding weather, water and humidity resistance, Permabond ET503 makes a handy addition to any turbine repair worker’s toolbox. One of its standout features is its ability to fully cure at temperatures as low as 5°C, meaning that any bonding work can be carried out on-site and will cure rapidly with fast strength development.
Ready to meet the challenges of the future
Adhesives will continue to be the helpers powering the green transition as we move closer and closer towards our shared goal of net zero emissions. As green technology continues to develop and unfold, innovative solutions will need to be found to meet the challenges and opportunities brought by these technologies. We, for one, can’t wait to do our bit.